Induction joining uses heat energy to create expansion in the material which can then be used to join a customized component. The process has recently gained particular importance in electric motor production. Induction heating is used for shrinking shafts into the rotor's magnetic laminated core and for joining the stator laminated core.
Induction joining
Heating for the mobility of the future
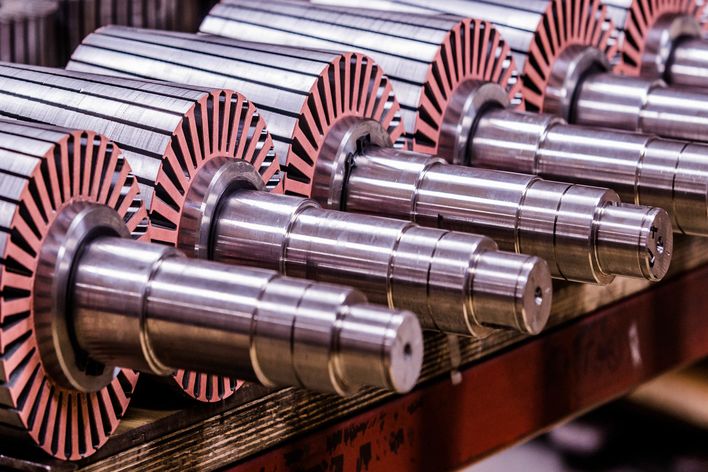
Induction joining significantly reduces heating times compared to indirect heating methods and is therefore more flexible and has a higher automation capability within a process. Temperature homogeneity throughout the laminated core's cross section is vital and must be achieved in the shortest possible cycle time. By using numerical simulation at TRUMPF Hüttinger, the heating times required and the optimum inductor geometry can be determined with extreme precision. This enables the generator power to be optimized and ensures the number of heating stations to be used is reached. Medium-frequency generators from TRUMPF Hüttinger combined with temperature measurement technology from SENSORTHERM deliver the required power reliably and reproducibly.
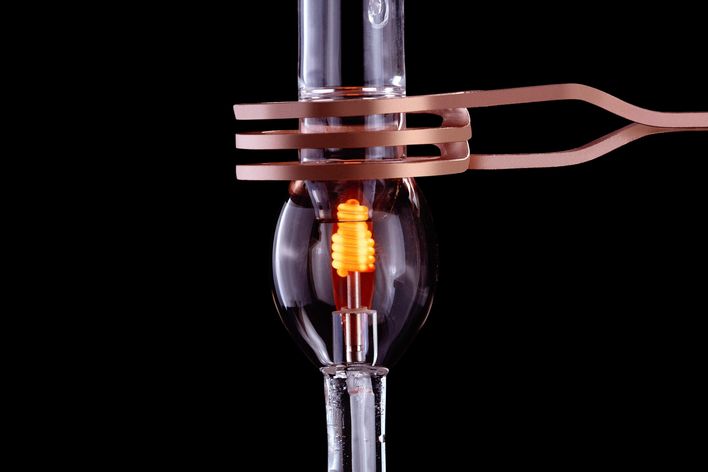
Glühen
Unhardened workpieces are used for annealing. They are heated and maintained at a specific temperature and generally followed by slow cooling. All annealing processes require uniform heating across the surface and penetration depth. Different types of annealing exist such as normalizing, stress-relief and soft annealing.
Products
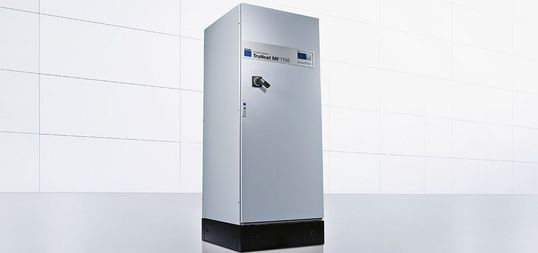
The combination makes it unique