What do autonomous machines mean for your production?
The age of intelligent production is already underway. TRUMPF machines are increasingly independent in their operation; they analyze and regulate processes. With your help, malfunctions can be prevented, and productivity can be increased. Employees can already be supported and relieved during many operations even today. Laser cutting will also become easier and less stressful in the future. Interested in learning the advantages that integrating autonomous and partially autonomous technologies can bring to your 2D laser processing? Click on the green dots in the image to find out more.
1. Fewer reject parts
Nip rejects in the bud: the sensor system can detect low quality materials or contaminations, thereby preventing cutting flaws before they occur.
2. Intuitive machines
Many malfunctions are detected or prevented through intelligent assistance systems. The Touchpoint HMI user interface allows machines to be operated more intuitively. Additional autonomous laser cutting functions can also be simply installed via software updates in the future
3. Transparent processes
This is how free of stress work can be: information or error messages are sent quickly and simply on the go, to a tablet or smartphone. The operator is informed whether manual intervention is required.
4. Relieved operators
While the cutting process is running smoothly, the operator has time for other tasks, for example material logistics or work preparations. This enables maximum productivity and machine utilization.
5. Error-free night shifts
Partially autonomous functions and automation components allow for stable production with minimal monitoring – even during night shifts with fewer personnel.
6. Maintenance and setup can be planned
In the future, it will be possible for autonomous laser cutting machines to recommend and control maintenance, as well as diagnose setup requirements on their own. Our services already allow easy ordering and quick availability of consumables.
7. Speeds far beyond default values
Active Speed Control renders the need to take buffers into account redundant. The sensor system allows the machine to work as quickly as possible, and with as much process reliability as necessary, respectively. Often speeds are achieved which are significantly higher than the default values contained in the cutting data.
8. Automatic post-production
In the future, highly autonomous and fully autonomous laser cutting machines will automatically determine restart strategies after remedying a malfunction. This enables automatic post-production.
9. Less reworking
Active Speed Control determines the optimal feed rate and adjusts this if required, even if sheet thickness varies. In many cases this reduces the amount of burr and dross build-up.
Something to consider
Even now we can look back on numerous milestones on the path to autonomous machines. This includes machine functions and assistance systems such as Smart Collision Prevention for collision avoidance, Smart Nozzle Automation, the automatic nozzle changer, as well as Smart Beam Control for intelligent laser beam monitoring. Development is nowhere near finished however, as demonstrated by ground-breaking developments such as the TruLaser Center 7030 full-service laser machine, or the Active Speed Control system for adaptive feed control. It will take a few years to reach full autonomy. Networked production environments and artificial intelligence (AI) will play an important part here.
Every company with a goal of keeping a sharp competitive edge in the age of digitalization achieves positive results through the automation of processes and the implementation of autonomously operating machines. Intelligent automation solutions for example, create the basis for cost-effective production and offer many advantages in terms of efficiency and transparency. But what good is the fastest machine if, for example, parts tilt? Intelligent assistance systems are the solution for many future challenges. Idle times can quickly take up half the working time of 2D laser cutting machines; this is how long it takes to equip, sort, or rectify malfunctions. Autonomously producing laser machines are able to prevent and rectify malfunctions on their own.
An increase in autonomy leads to a decrease in part costs. This is because fewer cases of malfunctions occur during production in general, and if they do occur, they are immediately detected and remedied by the machine – with operator support if required. This has a positive effect on output. Additionally, a significant decrease in rejects is produced. Active Speed Control proactively prevents cutting interruptions caused by fluctuating material quality, for example. This, for example, will prevent the undetected production of reject parts.
Production without malfunctions and rejects is desirable, but not quite realistic; the goal is to decrease the number of items that go to the scrap container. There will, however, always be materials and qualities which are only suitable for precise laser cutting under certain conditions. Whether produced parts require reworking is always dependent on the application. Burr and dross formation cannot be entirely eliminated. We are, however, working towards the goal of using the file as rarely as possible.
Active Speed Control is the latest TRUMPF development on the path to autonomous machines, and provides the entry to partially autonomous laser cutting. It makes parts production more robust, transparent, independent, and most of all, more productive. This is enabled through constant monitoring of the cutting process. With a live-view through the nozzle, the sensor system monitors the light that is emitted during material welding. Based on this so-called process light, it determines whether the welding is going according to plan, identifies the fastest possible feed, and adjusts this if required – hundreds of times per second. This creates fewer rejects, more process reliability, and less operator involvement with the machine.
Absolutely not. Operator involvement with the machine is decreasing, but for good reason – they will no longer need to shoulder the burden of having to manually monitor the cutting process. This means that they are relieved. The necessity of manual intervention in critical situations is drastically reduced. Instead, the operator receives information (for example with the Active Speed Control system for adaptive feed control) on their mobile device, and can react accordingly. What's particularly advantageous is that the operator is now able to focus on other tasks, such as programming, or preparing for setup or maintenance. They always have absolute control, supported by the laser machine and its assistance systems.
Download brochure
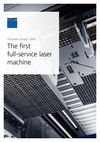

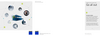
Curious about the future of laser processing?
What does autonomous laser cutting mean for your parts production? What benefits are there to you? Our 2D laser cutting experts would be happy to answer these as well as other questions.